Ascot Doors
Planning, Picking, Producing
Perfectly Painless.
Ascot Doors is a UK-based manufacturer specialising in industrial and commercial doors. With a reputation for quality, reliability, and national service coverage, Ascot Doors provides solutions to a wide range of clients from retail giants to logistics firms and public institutions.
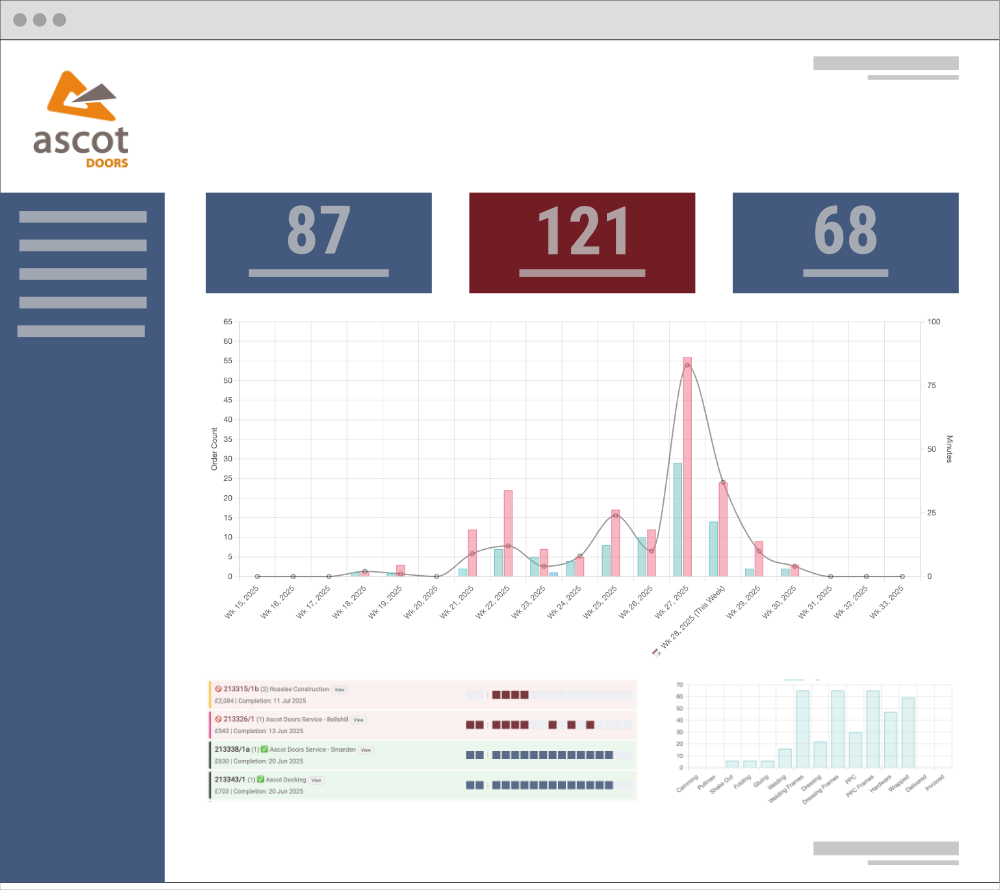
As Ascot Doors grew, managing production schedules, stock levels, and dispatch operations using spreadsheets paper, and legacy systems became increasingly inefficient. The team faced challenges including:
- Fragmented data across multiple sources
- Manual input errors
- Limited visibility into production bottlenecks
- Difficulty tracking job progress and forward planning
Accessible and easy to use, the new application replaces offline processes and removes outdated, manual spreadsheets to form a single source of their DataTruth™.
"Ascot got a system far better than we initially envisaged. We will only ever use Targeted for our future requirements."
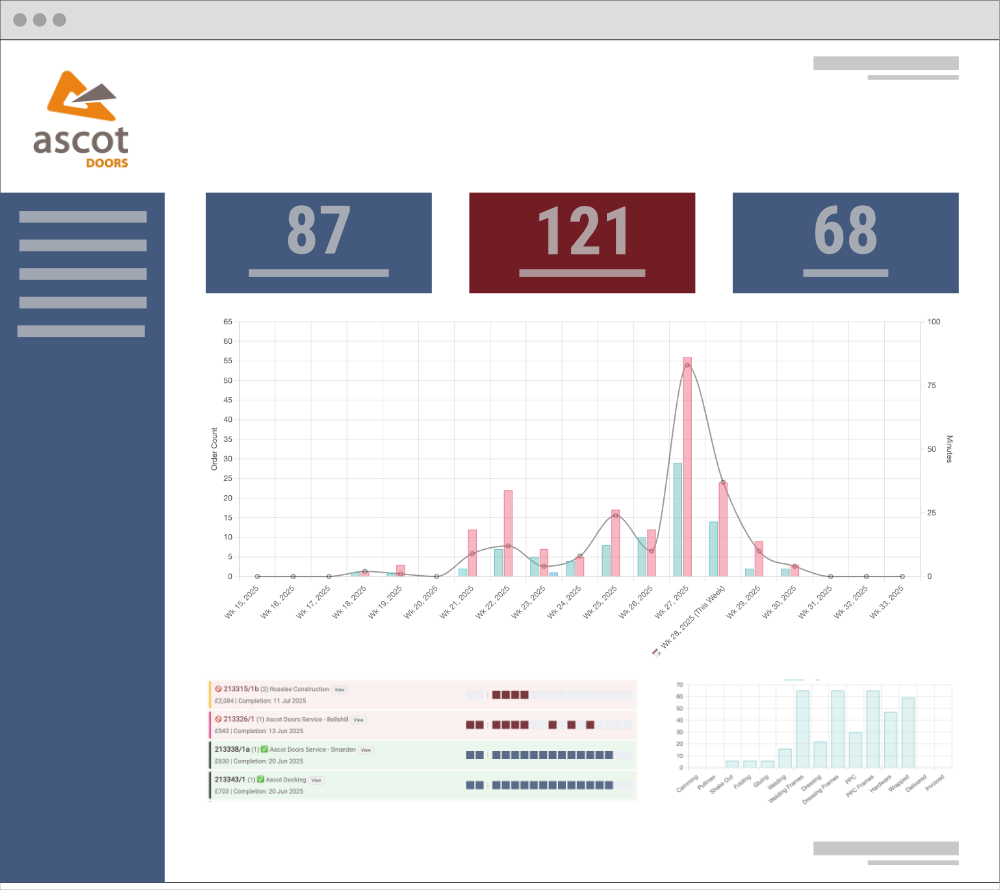
Real-time production management
- Live production scheduling
- Production capacity planning
- Instant issue escalation
- Contextual notes
- Centralised files
- Improved accuracy and decision making
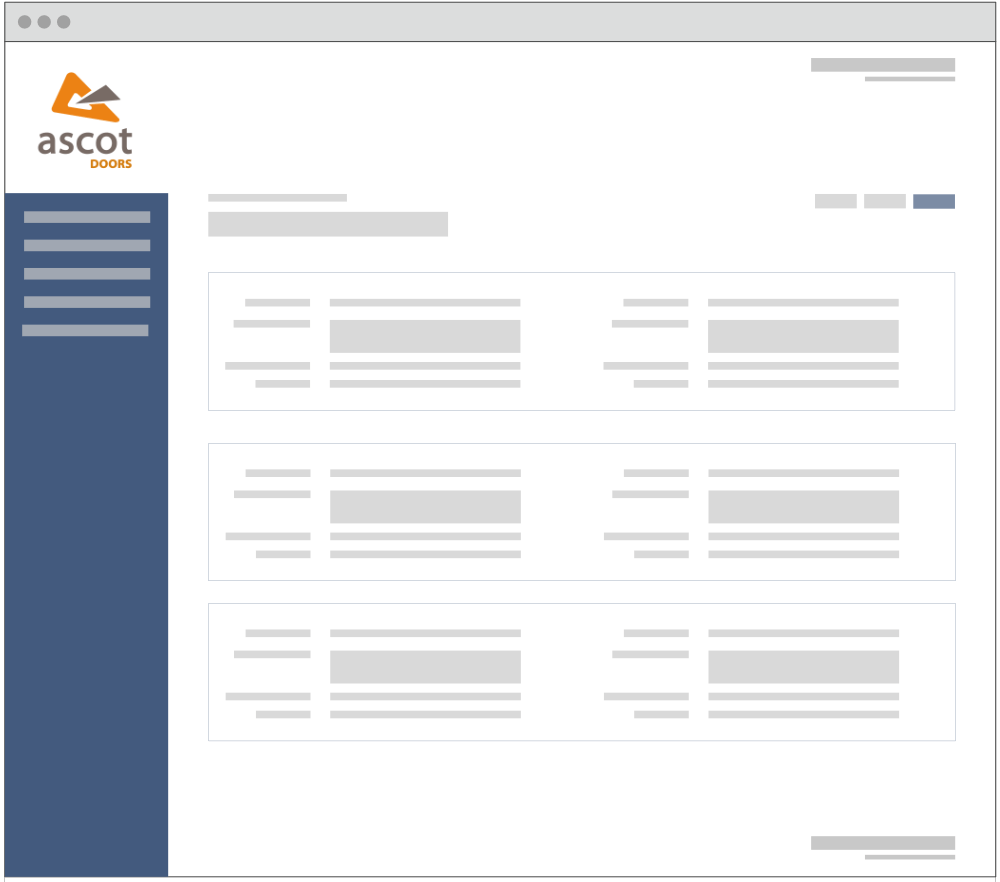
Every door, every time
- Each door has its own unique digital profile
- Door type defines the applicable production stages and options
- Key attributes like “Fire Rated Door” and “Special Instructions” are prominently flagged 🔥
- Technical drawings, sign-offs, and client documents are with each door
- Entirely paperless, fully audited
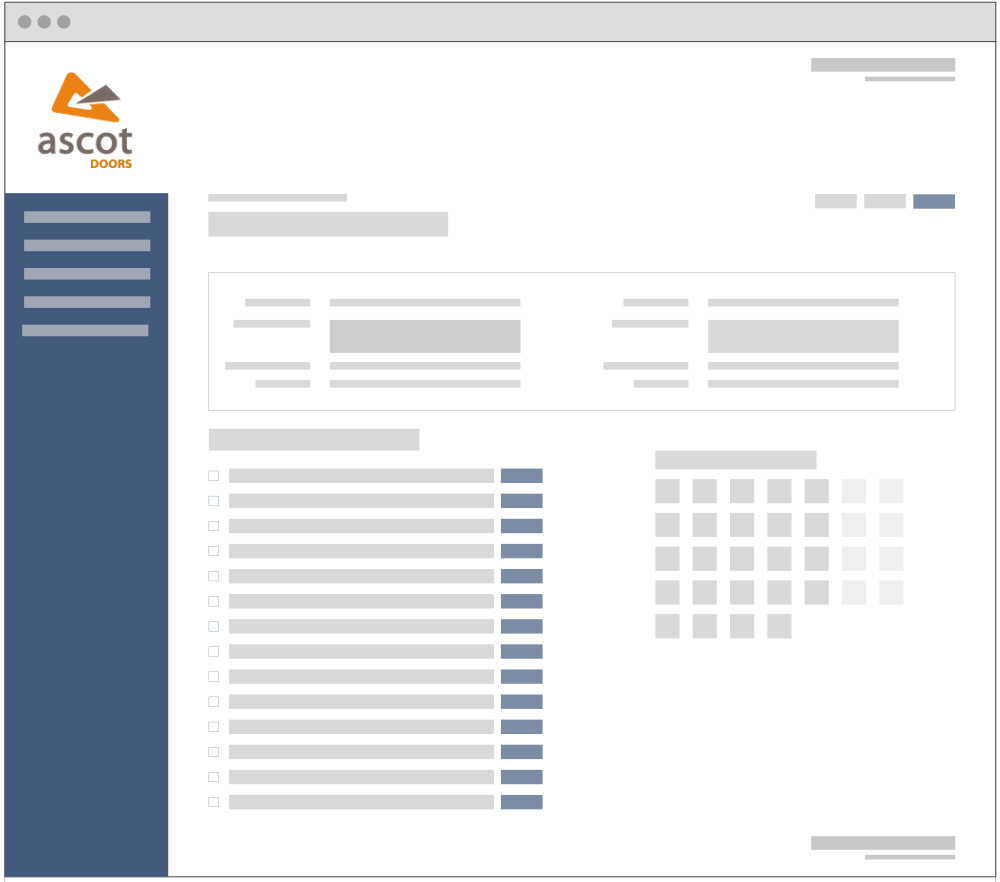
Dispatch optimisation
- Load schedule
- Clearly marked order statuses
- Managed sales/distribution areas
- Delivery hold notifications
- Stock picking optimisation by dispatch date
Ascot engaged with Targeted to upgrade our production management software.
Shaun was exceptional throughout and had a vast knowledge of production scheduling which resulted in Ascot getting a system far better than we initially envisaged.
— Danny Powell, Director
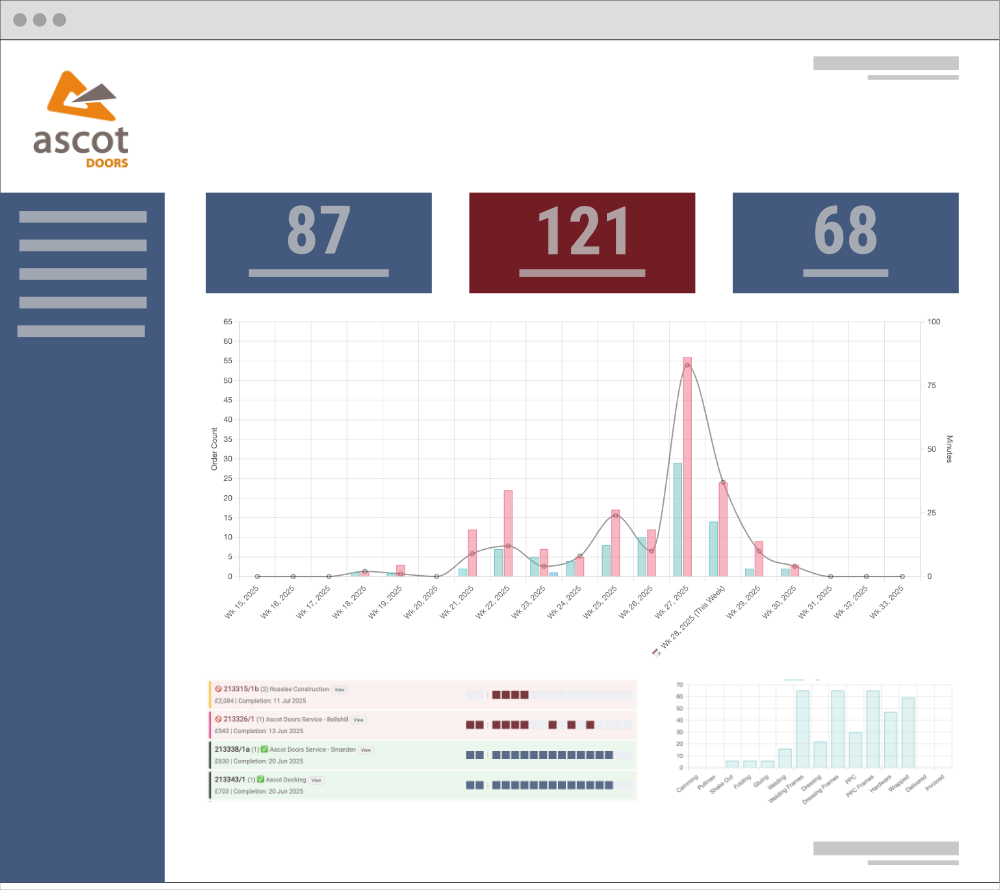
Real-time production management
- Live production scheduling
- Production capacity planning
- Instant issue escalation
- Contextual notes
- Centralised files
- Improved accuracy and decision making
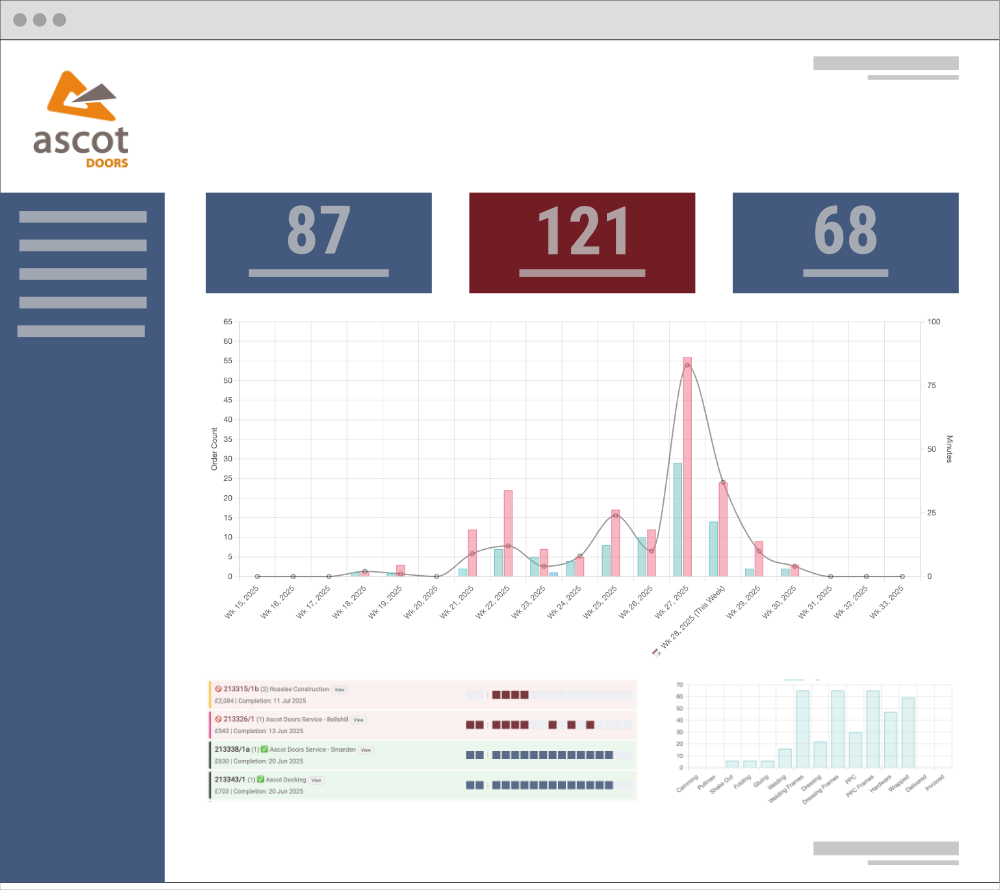
Work in Progress (WIP) reporting
- Real-time, accurate Work in Progress
- Calculations based upon door type
- Easily roll back to previous periods for audit
We have been given a high-quality, user-friendly product that will immensely improve our business.
We will only ever use Targeted for our future requirements.
— Danny Powell, Director
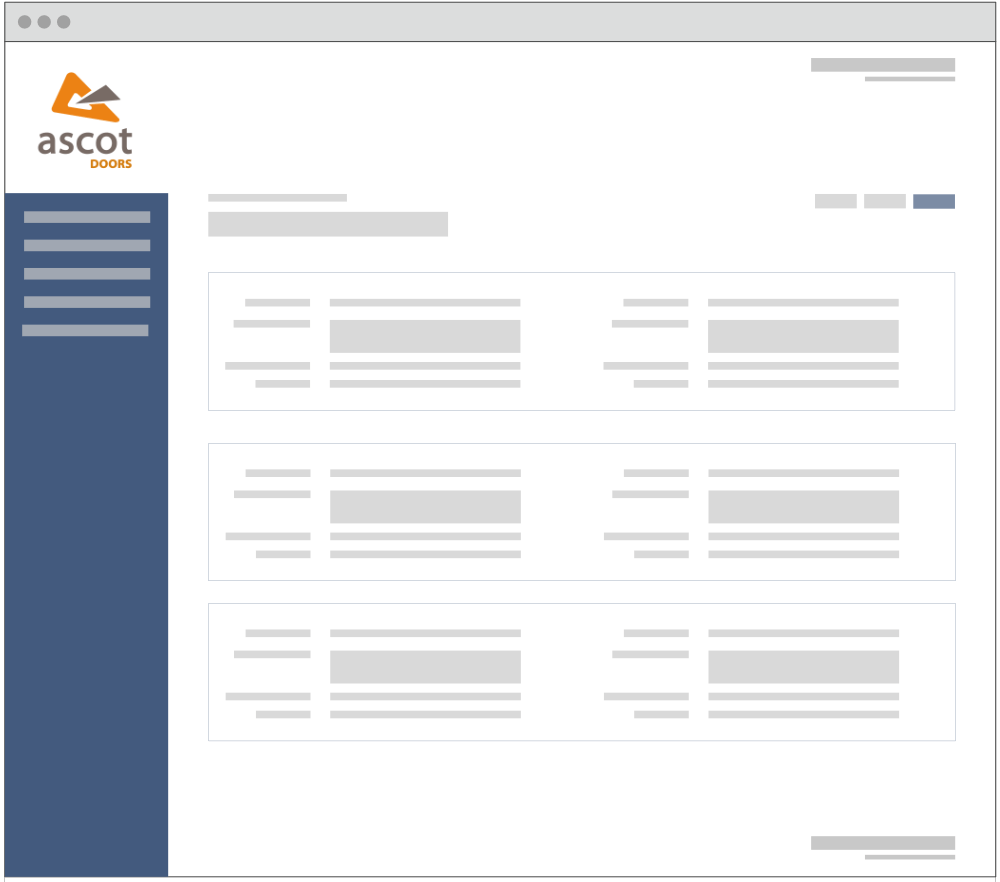
Stores and kit management
- Working backwards from dispatch, the system calculates when kits need to be picked
- Reduces delays from missing parts and ensures timely replenishment
- Improved traceability and accountability
- Forward workload planning
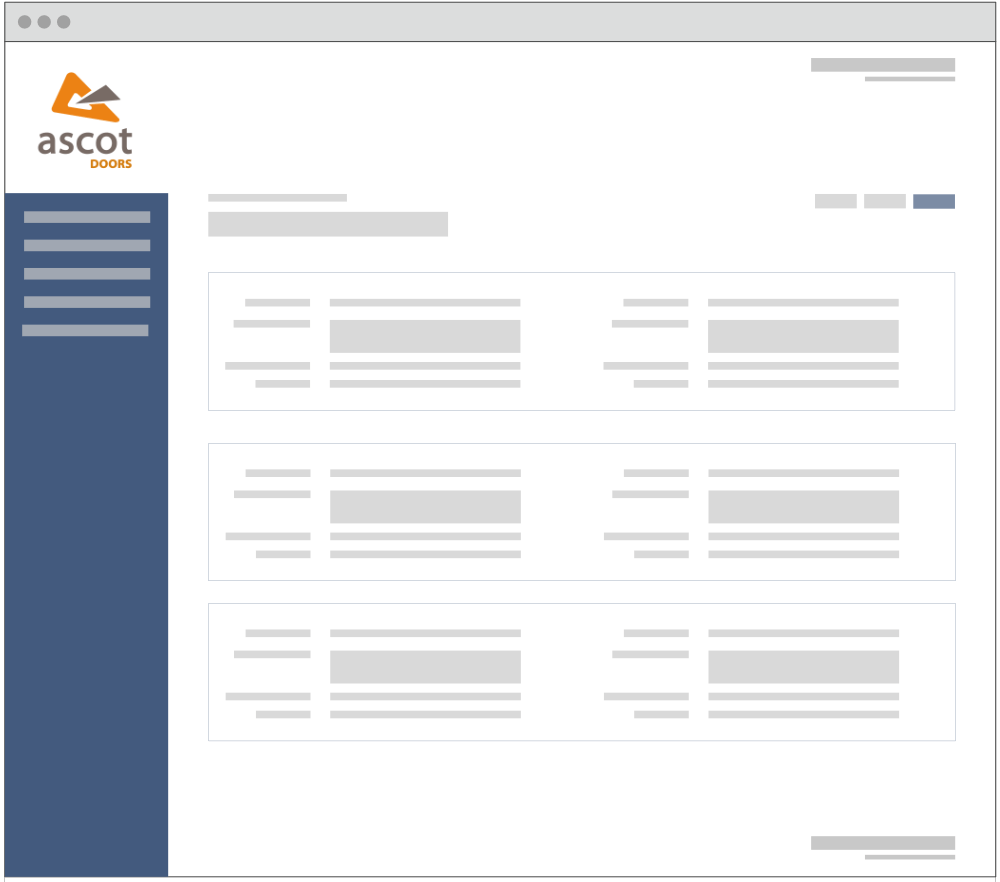
Document & File Management
- Drawings, certificates, customer specifications, and QA forms can be uploaded per door
- No more physical job folders or drawings
- Accessible by any authorised user from any device
- Always up-to-date information on the shop floor
- Remotely access and update
- Reduces carbon footprint
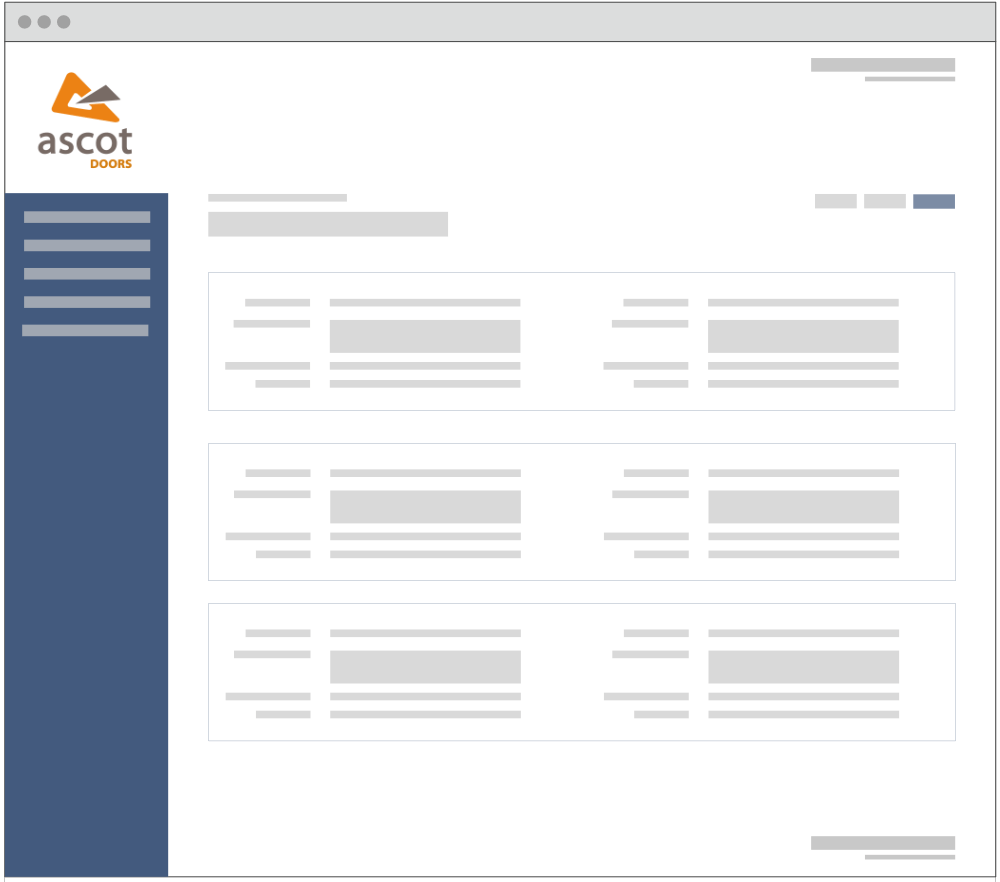
Full audit trail
- Every change is recorded: who did what and when
- Tracks updates to door records, notes, drawings, kit status, and dispatch info
- Provides a clear timeline of actions for each job
- Quality assurance, compliance, and accountability
- Helps identify where and when errors were introduced
- Supports continuous improvement
- No more finger-pointing — just facts
Nobody misses the paper and spreadsheets.
Powered by 100% renewable energy 🍃